Forging
What Is forging?

What is the purpose of forging?
The purpose of forging is to create metal parts. Compared to other manufacturing methods, metal forging produces some of the sturdiest manufactured parts available. As metal is heated and pressed, minor cracks are sealed, and any empty spaces in the metal close.
The hot forging process also breaks up impurities in the metal and redistributes such material across the metalwork. This vastly reduces inclusions in the forged part. Inclusions are compound materials implanted inside steel throughout manufacturing that cause stress points in the final forged parts.
While impurities should be managed during the initial casting process, forging further refines the metal.
Our forging product

The pounding action of forging deforms and shapes the metal, which results in unbroken grain flow. This causes the metal to retain its strength. Ancillary effects of this unique grain flow include the elimination of defects, inclusions, and porosity in the product. Another advantage of forging is the relatively low costs associated with moderate and long production runs. Once the forging tools have been created, products can be manufactured at relatively high speeds with minimal downtime.There are two main types of forging: hot and cold.
Rolled Ring Forging
Close Die Forging
Open Die Forging
Fully Machined Component
rolled ring forging

CM TECHNO WEB has advanced capabilities for the manufacture of ring rolled forging.
- CM Techno Web produces rolled rings
- OD = Ø 100 mm to Ø 1200 mm,
- Height = 25 mm to 300 mm
- Weight In Kg. 1 Kg. to 300 Kg.
Our ability to optimize manufacturing and process capabilities, while offering the “insurance” back-up of 6 ring mills, allows us to deliver the highest quality ring to you in the least amount of time.
Rectangular or profile rings as per customer’s requirement.
Rings are made from Carbon Steel, Alloy Steel, Structural & Tool Steel, Low Carbon Steel & Stainless Steel.
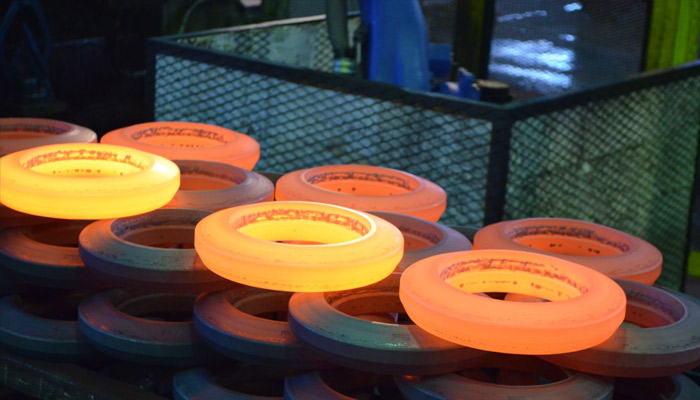
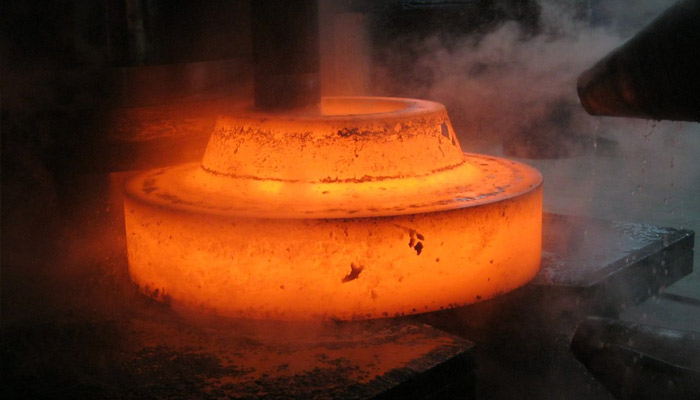
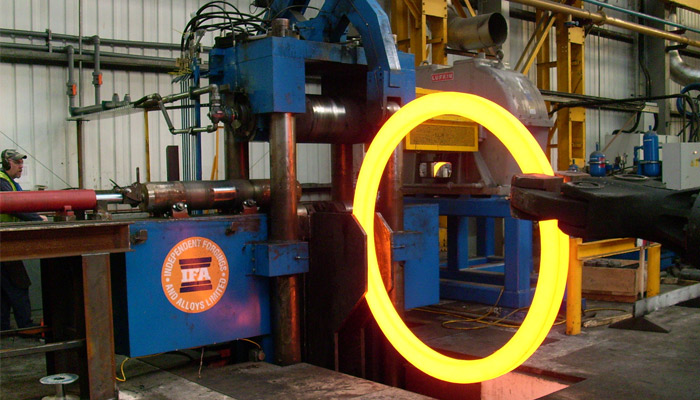
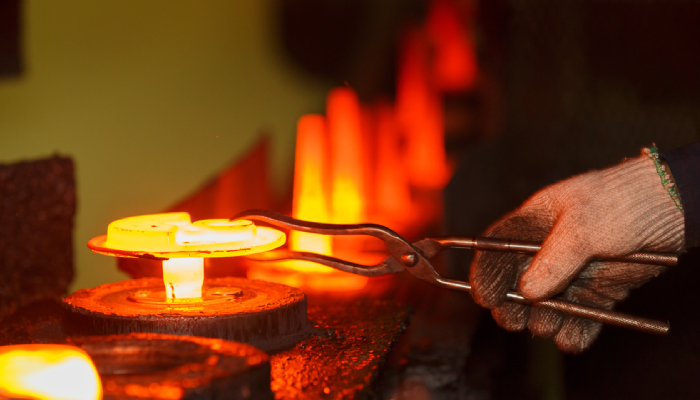
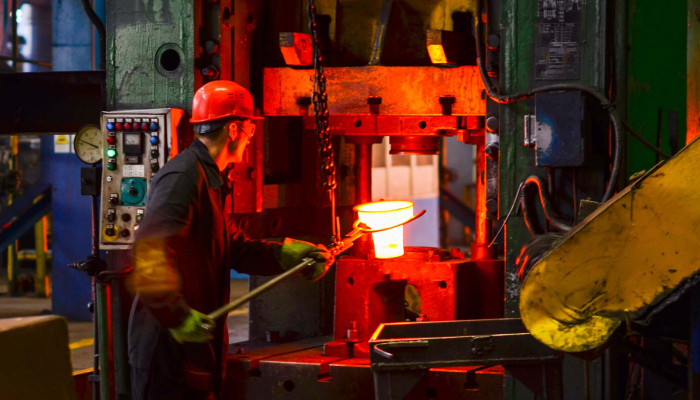
Close Die Forging

CLOSED DIE FORGING is the process whereby this deformation is confined within a shaped cavity in the dies to achieve a desired engineering configuration. Depending on such factors as complexity, tolerances, economics and performance, the dies required to produce Closed Die forgings range from complex multi-segmented PRECISION wrap dies to simple two-piece CONVENTIONAL top-and-bottom dies.
Cm Techno Web supplied below industries.
Bearing Races, General Engineering Product, Hub, Differential Case and Cover and Transmission parts
Gears, Rollers, Idlers, Crane Wheels,
Traction Gears and Bearing Shells
4.Oil And Gas
Metal Gasket, Valve Bodies, Gates, Flanges, Discs for Valves and Forged Fittings
Open Die Forging

OPEN DIE FORGING involves the shaping of heated metal parts between a top die attached to a ram and a bottom die attached to a hammer anvil or press bed. Metal parts are worked above their recrystallization temperatures-ranging from 1050°C to 1250°C for steel-and gradually shaped into the desired configuration through the skilful hammering or pressing of the work piece.
While impression or closed die forging confines the metal in dies, open die forging is distinguished by the fact that the metal is never completely confined or restrained in the dies. Most open die forgings are produced on flat dies. However, round swaging dies, V-dies, mandrels, pins and loose tools are also used depending on the desired part configuration and its size.
Although the open die forging process is often associated with larger, simpler-shaped parts such as bars, blanks, rings, hollows or spindles, in fact it can be considered the ultimate option in “custom-designed” metal components. High-strength, long-life parts optimized in terms of both mechanical properties and structural integrity are today produced in sizes that range from a few pounds to hundreds of tons in weight. In addition, advanced forge shops now offer shapes that were never before thought capable of being produced by the open die forging process.
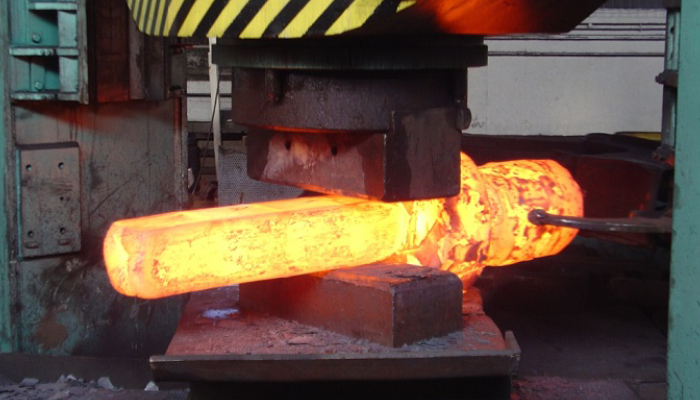
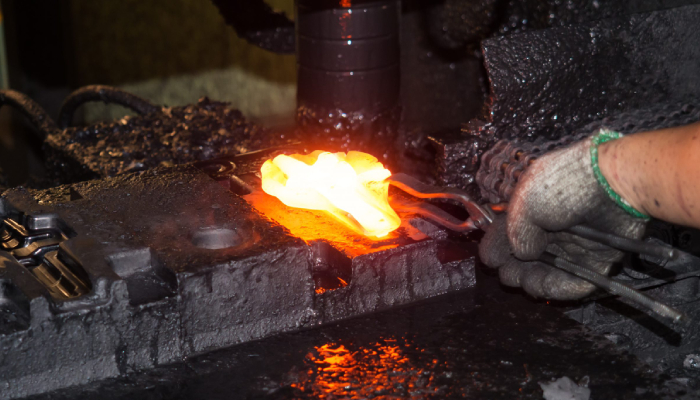

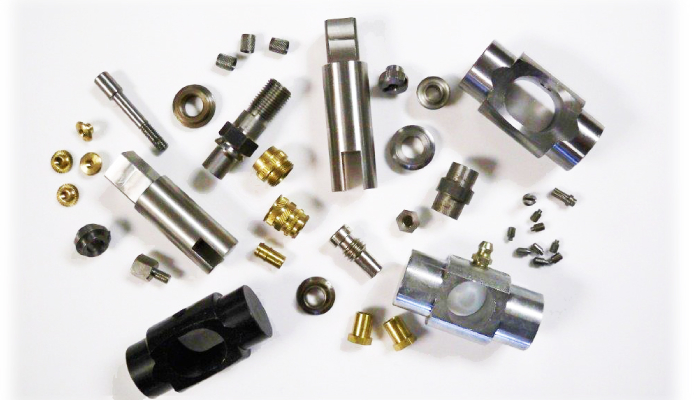
Fully Machined Component

At Cm Techno Web we offer a full range of in-house machining options to take your forgings to near-finished dimensions.
A combination of over 26 CNC machine & 4 VMC Machine gives us the ability to turn, mill, or bore your parts as specified, with finishes ranging from 500 to 16 RMS.
For CNC Machine Capacity Up-to 100 Kg. Single Pc.
For VMC Machine Capacity Up-to 100 Kg. Single Pc
Cm Techno Web supplied in below industries with fully machined component :
- Automotive Parts
- Transmission Gears & shaft
- Hubs & Sleeves
- Bearing Races
- Valve Body
- Pump Parts
- Railway Bearings & hubs
- And many more as per customer’s requirement.
What are the different forging processes?
Beyond basic hot and cold forging, many specific processes exist. This broad range of processes can be grouped into three primary umbrella groups: Draw forming decreases the width of the product and increases length. Upset forging increases the width of the products and decreases length. Compression forming provides forging flow in multiple or customized directions.These three categories entail many different specific types of metal forging methods.